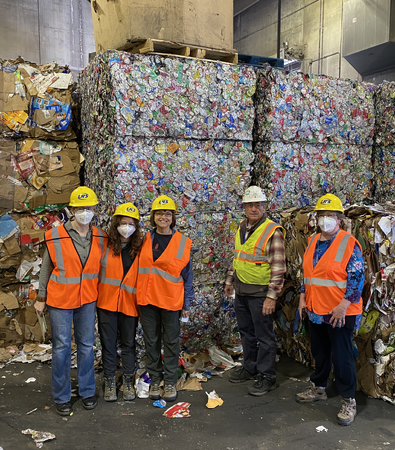
Kane County Board Members Witness Recycling in Action
Kane County Connects Staff/ Kane County Recycling Coordinator Clair Ryan 10/12/2022 1:00PM
Recently, members of the Energy and Environmental Committee and staff from the County’s Department of Environmental and Water Resources toured LRS’s Heartland recycling facility in Forest View. Heartland is a materials recovery facility (or MRF, pronounced “murf”) that takes mixed recyclables coming from curbside carts and office building dumpsters and sorts them into single-material bales that are sold for recycling. LRS co-founder and Managing Partner, Joshua Connell, walked the group through each step in the process.
Here’s what committee members and staff learned:
After a recycling cart is emptied, the curbside recyclables are taken to a transfer station. If your municipality or township is served by LRS, most consolidated recycling material is currently transported to Heartland. The other large haulers, including Groot/Waste Connections and WM (formerly Waste Management) also have MRFs in the greater Chicago area. Transfer trucks drop their loads onto a tipping floor at the MRF where a massive excavator shifts material into towering piles to make room for more.
From the tipping floor, mixed recyclables are fed onto a conveyer belt equipped with a large, rotating drum. Limited clearance under the drum prevents really large three-dimensional items from making it onto the line. According to Kane County Recycling Coordinator Clair Ryan, if an item is not made of cardboard and is bigger than the largest laundry detergent bottle, it shouldn’t go into curbside recycling. Next, the conveyor belt traverses the “pre-sort line” where workers manually pull wish-cycled items off the line. The belt is fast moving and workers are mostly looking for and grabbing the items most likely to clog up or damage equipment. These include plastic bags, wires, chains, clothing, clothes hangers etc. (in industry jargon, these are all “tanglers”), large pieces of scrap metal, lithium ion batteries, and just straight up trash. Workers drop the plastic bags and scrap metal through designated chutes in the floor where they are collected and recycled separately.
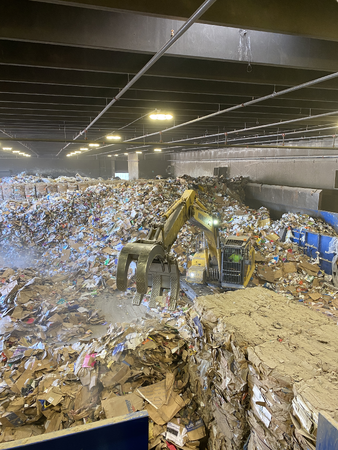
Next, the mixed materials directed to a machine with large, rotating shafts. Corrugated cardboard pieces pass over the top of the shafts, while all containers and smaller less rigid paper items fall through. Now there are two streams of material - one mostly cardboard, and one with everything else. The cardboard stream goes past a manual quality control line, where workers pick out contamination to improve the purity and value of the finished corrugated cardboard bales. The cardboard is baled up and sold
on.
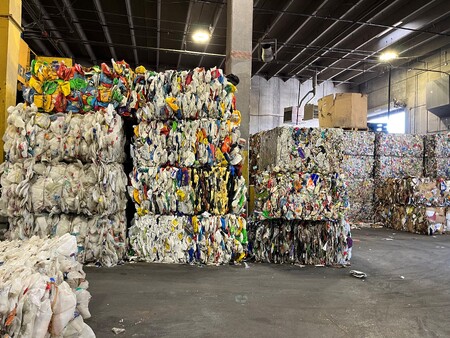
The rotating shafts of the cardboard sorter smash up all the glass at the MRF. Directly underneath that machine is an additional “fines” screen, which removes all small items less than 2” in any dimension, including glass shards, bottle caps, scraps of paper, plastic utensils etc. Metal bottle caps are pulled out and separated by a powerful magnet. Unfortunately, the much of the mixed glass is contaminated with plastic and paper - if not for the tinkling sound heard, it’s hard to even recognize the pile as mostly glass. According to Recycling Coordinator Ryan, individuals can help solve this problem by leaving plastic bottle caps ON their containers when you recycle. It is also important not to “wish cycle” very small items like plastic utensils, straws and shredded paper. Most of these should go in the trash. Shredded paper can also be dropped off at Kane County Recycling Centers.
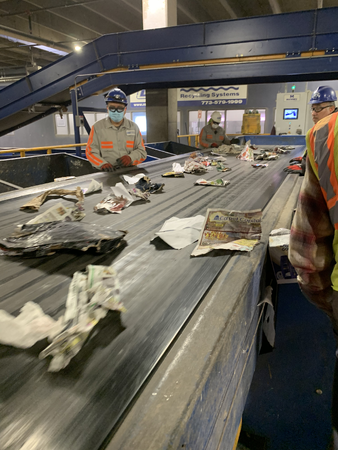
The material stream, now cleared of glass and small items, continues on to two more linked pieces of equipment - a paper screen and a ballistic sorter. The screen - called a star screen- has rotating star-shaped disks while the ballistic sorter is made of large, rapidly shuffling metal plates. The motion of these machines causes paper and other two-dimensional items to travel “uphill” while three-dimensional containers to fall down. Recycling Coordinator Ryan, reminds people not to crush plastic and metal containers or food and beverage cartons, because it prevents them from being sorted properly by the equipment. The final stream of two-dimensional material, which is mostly paper, is quality checked by workers, and then it too goes for baling.
Now the material stream is made up mostly of containers. An industrial magnet and an eddy stream current are used to separate out steel and aluminum respectively. Heartland has both optical sorters and a robot suction arm with artificial intelligence for sorting. The County tour group watched an optical sorter that was set to identify PET (a.k.a. Plastic #1 - the stuff plastic beverage bottles is made of). The sorter identifies the material by reading the light signature each item reflects, and when it “hits” on PET, it directs blasts of compressed air at these targets and knocks them off the line to be collected below (see this machine in action). The robot arm “sees” items with a camera and identifies them using the same characteristics a person would (color, shape, opacity, labeling, etc.). When the robot identifies the items, it’s instructed to look for, it uses its suction arm to pull each item off the line with impressive speed. When we were there, the robot was pulling aseptic and gable top cartons (the types of cartons used for dairy milk, plant milks, coconut water, juice boxes, soup, etc.), undyed HDPE (a.k.a. Plastic #2 - the stuff laundry detergent bottles are made of), colored HDPE, and aluminum foil items, and dropping them down separate chutes. While the County’s visitors couldn’t take their own video due to glare off the robot’s enclosure, the manufacturer has a video of the SamurAI robot working at LRS Heartland.
Items that remain on the line after all the sorting is done are typically classed as discards, though many MRFs, including Heartland, send their discards through the whole line system a second time to make sure everything that can be recycled is recycled. Ultimately, the final discards will be landfilled as trash.
When all is said and done, the Heartland MRF and others like it are producing and selling bales of PET bottles, clear and colored HDPE, aluminum, steel, mixed paper and cardboard that are remarkably uniform and clean considering the jumble of material that went in. At Heartland, this all happens within the span of five days, from an item being dumped on the tipping floor to leaving as part of a bale. The facility runs around the clock to sort through 110,000 tons of recyclables a year. Despite the combined forces of man and machine, MRFs can only do so much. Please take a minute to refamiliarize yourself with curbside recycling guidelines.
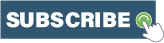